Sotek Engineering
Quality and Safety
Sotek Engineering Ltd has been assessed and certified as meeting the requirements of ISO 9001:2015
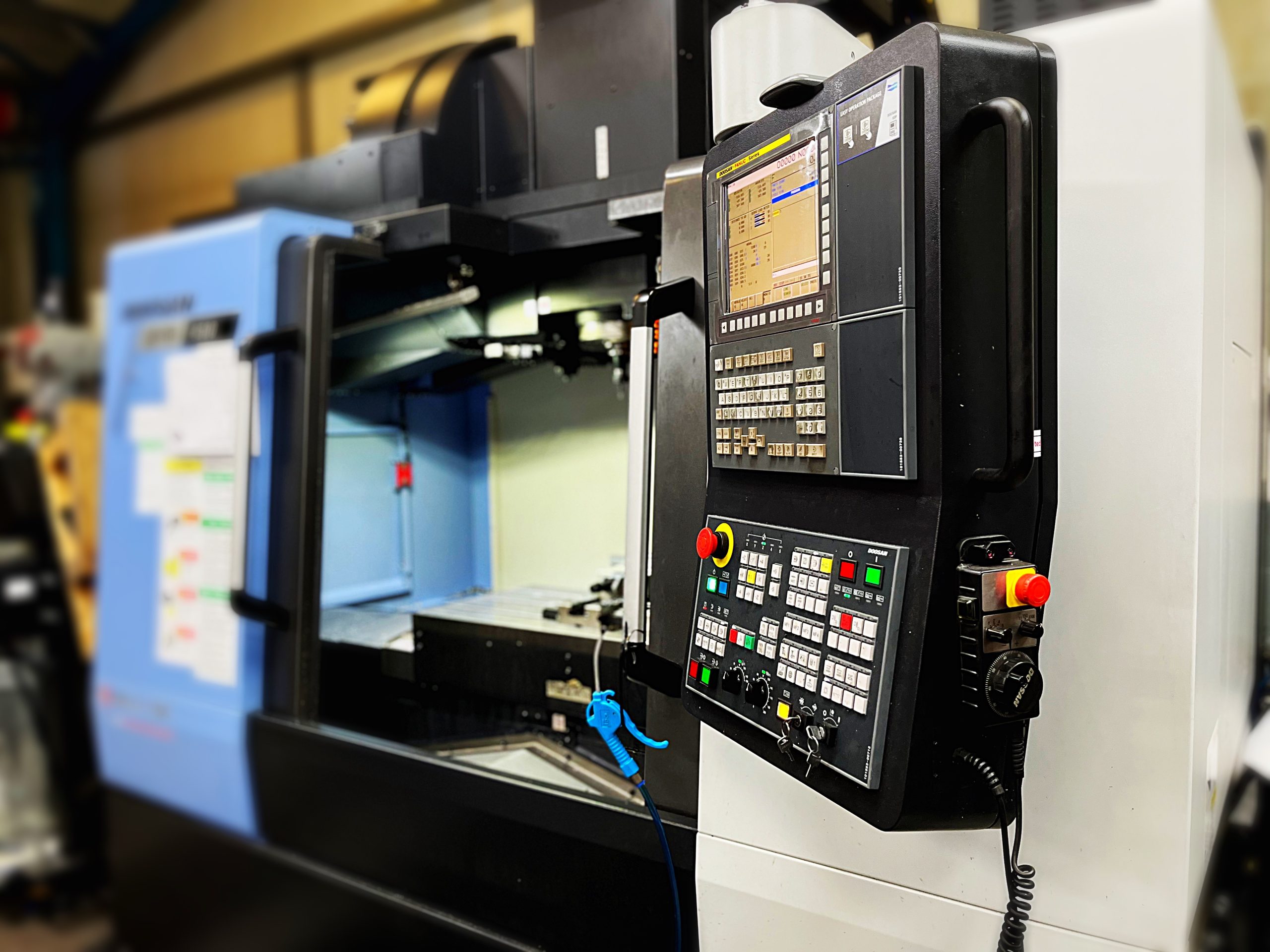
Quality
We have an exemplary record in delivering products with zero defects. To ensure this is maintained we ensure to use ISO 9001:2015 compliant quality management systems.
Our quality systems are the backbone of our manufacturing services and have helped us to improve our product development processes significantly. You can be assured of the highest quality possible as well as paperwork and traceability that meet industry standards.
Quality control is a critical aspect of CNC manufacturing, as it ensures that parts and components are produced to the required specifications, dimensions, and tolerances. Here are some of the quality control procedures that are typically used in CNC manufacturing:
First Article Inspection (FAI): A first article inspection involves the measurement and verification of a prototype or first production piece against the design specifications. This helps to identify any issues or discrepancies before mass production begins.
In-Process Inspection: In-process inspection involves inspecting parts at various stages of the manufacturing process to ensure that they meet the required specifications. This can include dimensional checks, visual inspections, and material testing.
Final Inspection: Final inspection involves a comprehensive inspection of the finished part to ensure that it meets all of the required specifications, dimensions, and tolerances. This can include measuring key features, checking surface finish, and performing functional testing.
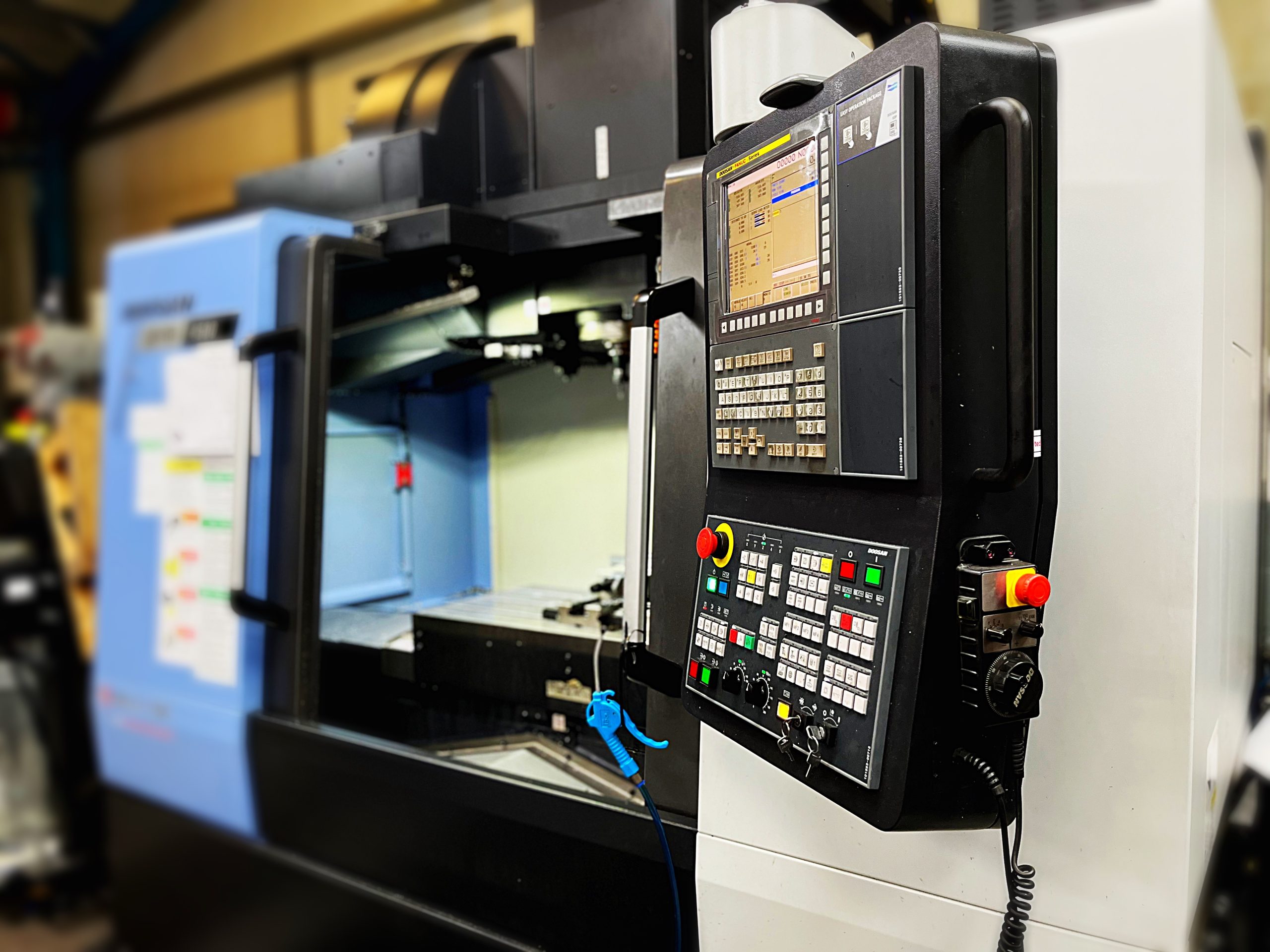
Quality
Statistical Process Control (SPC): SPC involves monitoring the production process to detect and correct any variations or deviations from the expected quality standards. This can help to improve process efficiency and reduce the likelihood of defects.
Calibration: Regular calibration of CNC machines and measuring equipment is essential to ensure that measurements are accurate and consistent.
Traceability: Traceability involves tracking parts and components throughout the manufacturing process to ensure that they are produced to the required standards and are traceable to their source materials and production processes.
Overall, quality control procedures are an integral part of CNC manufacturing and are essential to ensure that parts and components are produced to the required quality standards, resulting in higher customer satisfaction and lower costs due to reduced scrap and rework.
Health and Safety
At Sotek we are passionate about the health, safety, and welfare of all our employees and others (including visitors, contractors and the public).
Sotek is committed to the implementation of a Health & Safety Management System that complies with OHSAS 18001:2007. Where possible we ensure there is IOSH qualified managers available to support staff wherever necessary.
Health and safety in a CNC factory is crucial to ensuring the well-being of employees and the smooth operation of the business. Here are some key areas to consider:
Machine safety: CNC machines can be dangerous if not operated correctly. Proper machine guarding, emergency stop buttons, and lockout/tagout procedures should be in place to prevent accidents.
Personal protective equipment (PPE): Workers should wear appropriate PPE such as safety glasses, earplugs, and steel-toed shoes to protect themselves from flying debris, loud noise, and potential slips or falls.
Hazardous materials: Some CNC operations involve the use of chemicals or other hazardous materials. Employers should provide training on handling these materials, proper disposal, and ensure that employees have access to necessary protective gear.
Health and Safety
Ergonomics: Working with CNC machines often requires repetitive motions and long periods of standing, which can cause strain and injury. Employers should ensure that workstations are ergonomically designed, and employees have access to breaks and stretches to reduce the risk of injury.
Electrical safety: CNC machines require a significant amount of electricity to operate, and employees should be trained to recognise and avoid electrical hazards. Regular equipment maintenance and inspection can also prevent electrical issues from occurring.
Training and communication: Employees should be thoroughly trained on all safety procedures, including how to use machines, what PPE to wear, and how to respond to emergencies. Employers should also provide regular communication and feedback channels to promote a culture of safety and continuous improvement.
By prioritising health and safety in a CNC factory, employers can ensure a safe and productive workplace that benefits both employees and the business as a whole.
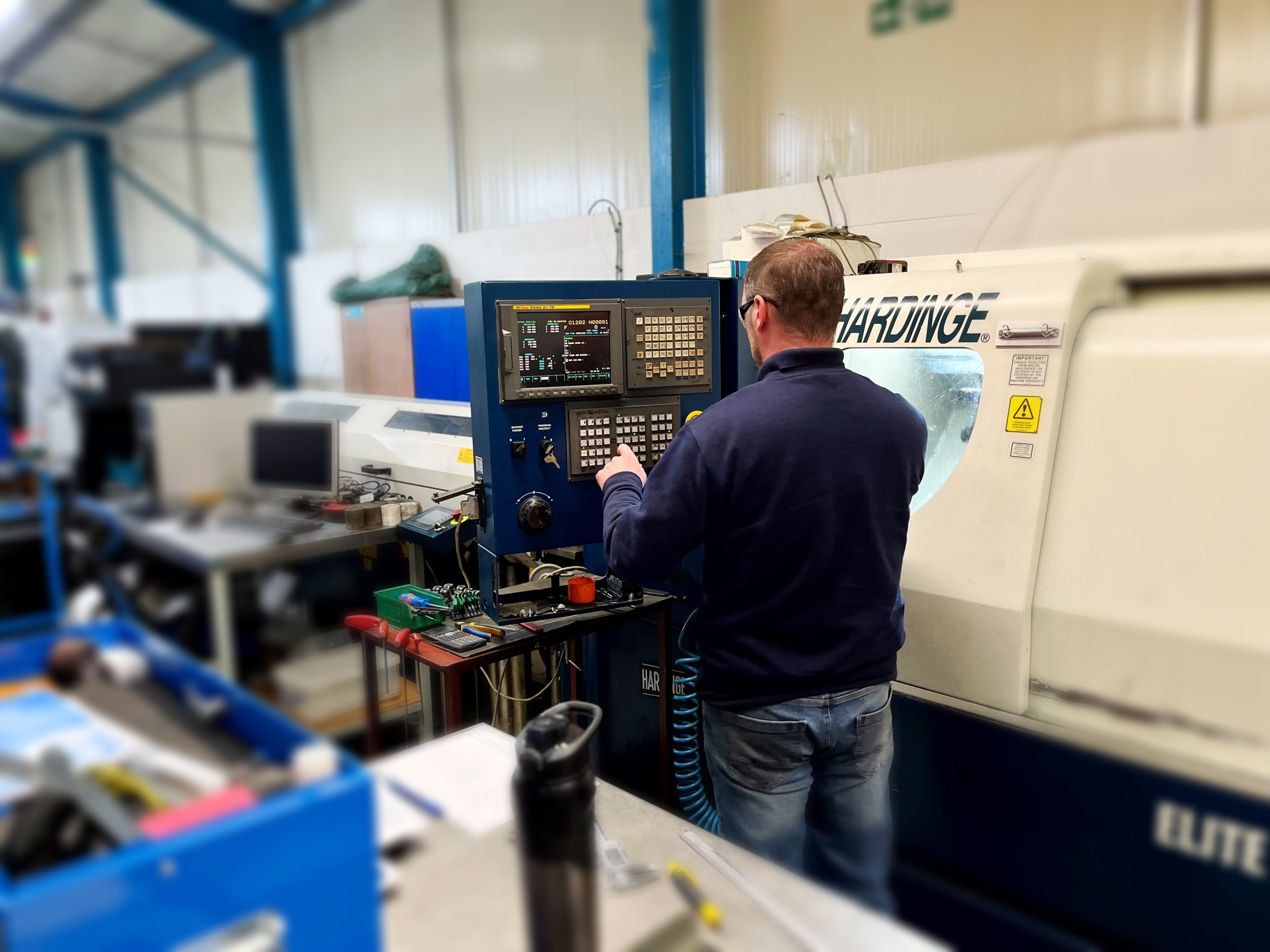
Environment
Sotek Engineering consider environmental matters to be of critical importance. They are a primary factor in our drive for world class standards and sustainable development by continuous improvement in our activities.
We recognise that our activities impact on the environment in a number of ways and it is our policy to minimise any adverse effects on the environment and the earth’s resources as well as safeguarding the health and safety of our employees and the general public.
Environmental considerations are essential for a CNC manufacturing plant to reduce its impact on the environment and promote sustainable practices. Here are some key areas to consider:
Energy efficiency: CNC machines require a significant amount of energy to operate, and optimising their use can reduce energy consumption and associated greenhouse gas emissions. Employers should consider using energy-efficient equipment and practices such as using variable frequency drives to control motor speeds, turning off equipment when not in use, and using LED lighting to reduce energy use.
Waste reduction: CNC manufacturing plants generate waste in the form of scrap metal, chips, and coolant. Employers can reduce waste by implementing a recycling program for scrap materials, using reusable containers, and implementing a closed-loop coolant system to reduce the amount of waste coolant generated.
Chemical management: CNC manufacturing plants may use chemicals such as lubricants, solvents, and cleaning agents. Employers should use environmentally-friendly products, minimise chemical use, and properly store and dispose of chemicals to prevent environmental contamination.
Water conservation: CNC manufacturing plants use water for cooling, cleaning, and other processes. Employers should consider using water-saving technologies such as low-flow faucets and recycling water for non-potable uses to reduce water consumption.
Environmental permits and regulations: Employers should be aware of environmental permits and regulations that apply to their facility, such as air emissions, wastewater discharge, and hazardous waste disposal. Compliance with these regulations is essential to protect the environment and avoid legal and financial penalties.
By implementing sustainable practices in a CNC manufacturing plant, employers can reduce their environmental impact, save resources, and promote a healthier and safer workplace for employees.