Sotek Engineering
Design
Design For Manufacture
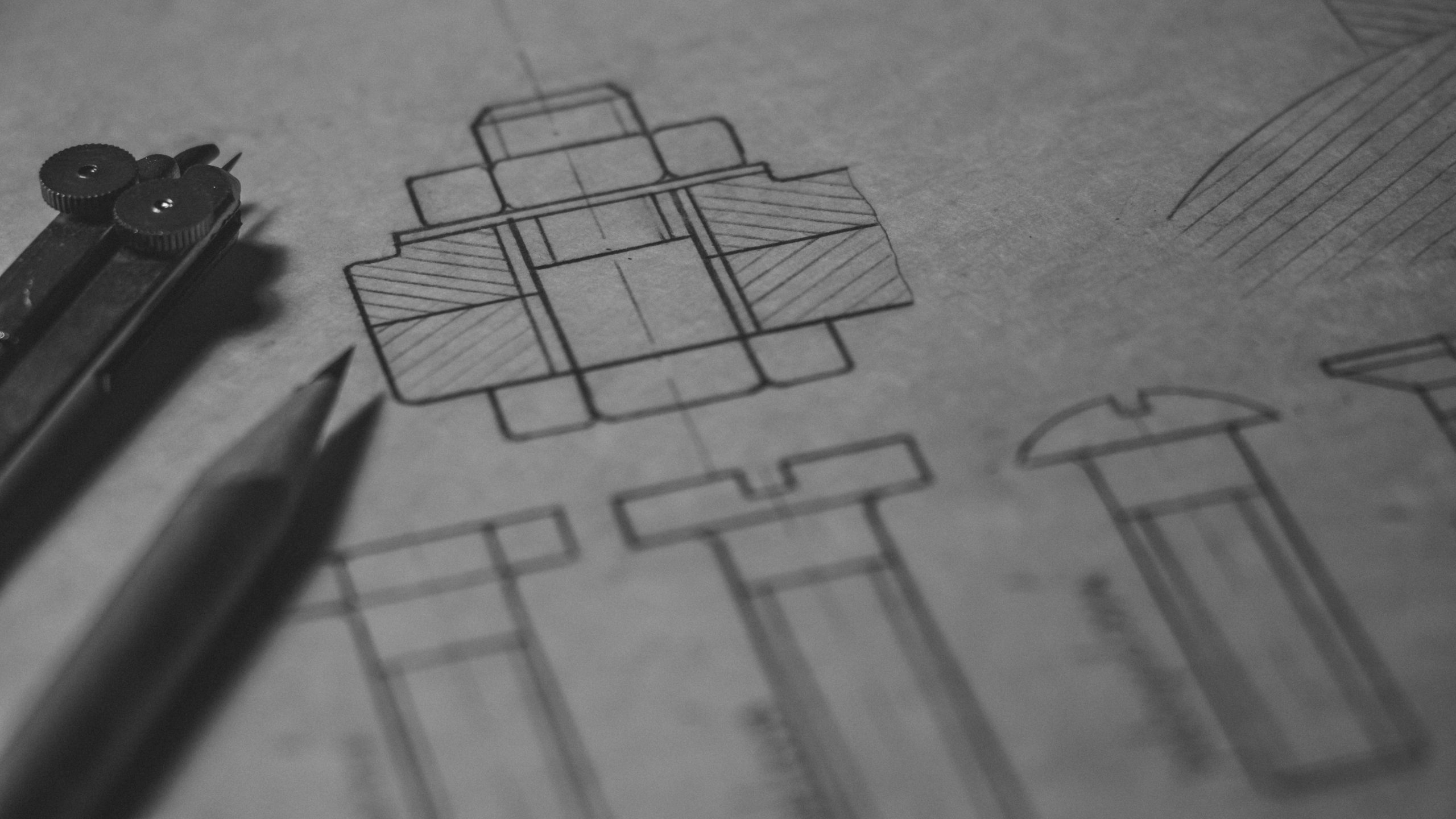
Design
Design for Manufacture (DFM) is an essential aspect of CNC (Computer Numerical Control) production, as it ensures that parts and components are designed in a way that can be easily and efficiently manufactured using CNC machines. Here are some important considerations for DFM for CNC production:
Material selection: Choosing the right materials for a part is critical in ensuring that it can be machined effectively. Materials that are difficult to machine or prone to warping, such as some plastics or certain metals, may need to be avoided or modified in the design.
Part orientation: The orientation of the part during the machining process can significantly affect the quality and efficiency of production. Designers should consider the orientation of features and how they will be machined, including tool access, clearance, and support.
Part geometry: Parts should be designed with simple and uniform geometries that can be easily machined. Complex geometries can increase machining time, which can result in higher production costs.
Design
Tolerances: Designers should be mindful of the tolerances required for the part and ensure that they are feasible to machine accurately using CNC equipment. Tolerances should be specified based on the functional requirements of the part.
Surface finish: Designers should specify the required surface finish for each part, taking into account the capabilities of the CNC equipment and the desired appearance or functionality of the finished part.
Assembly: Designers should consider the ease of assembly and integration of the parts into the final product. Parts that are difficult to assemble or integrate can increase production time and costs.
By considering these factors during the design phase, designers can optimise the design of parts for CNC production, resulting in faster production times, improved quality, and lower costs.
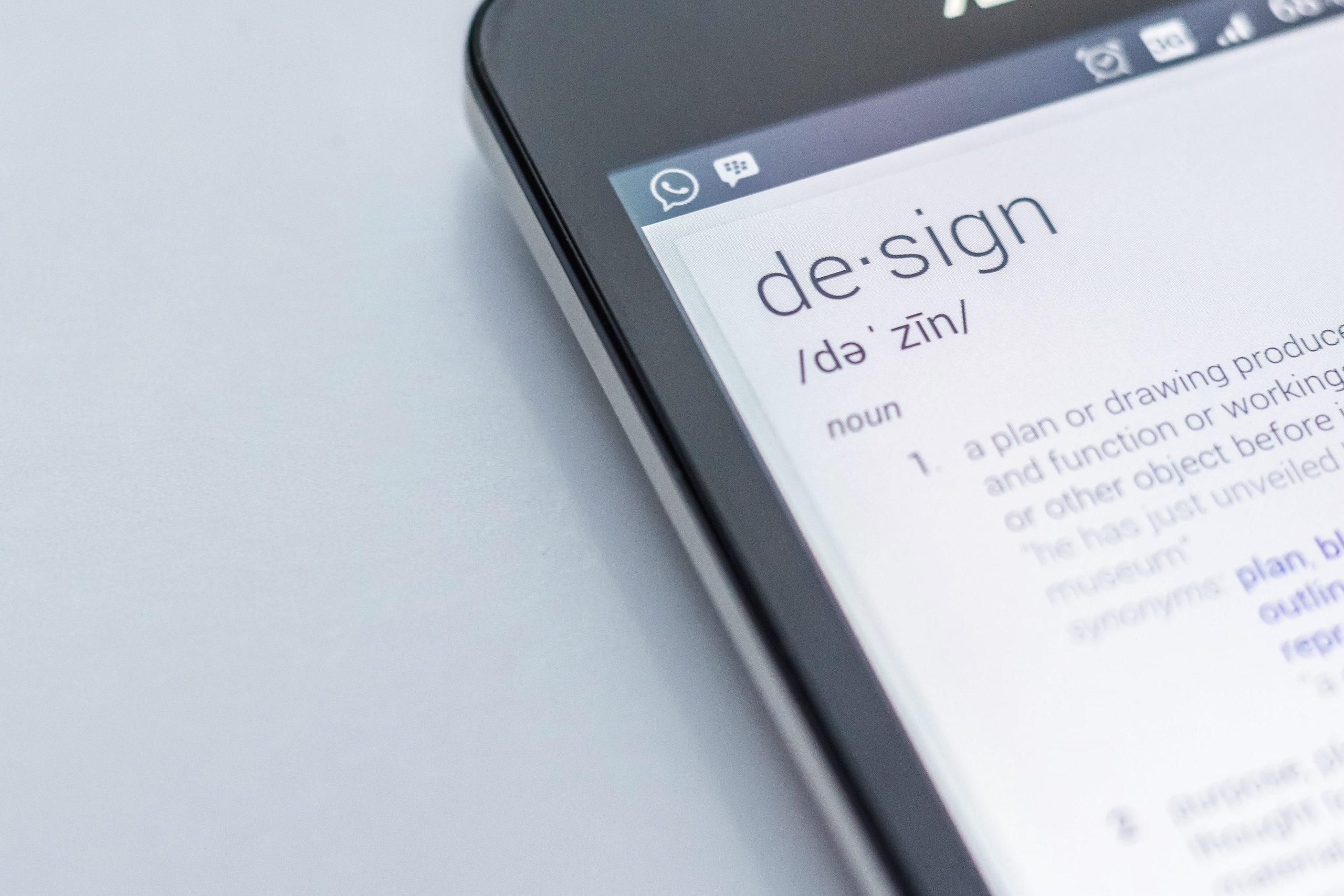
We follow these 6 steps to ensure the mechanical design is optimum:
Step 1. Outline The Concept/Problem
This will enable us to have a clear idea of what the problem is before it is overcome.
Step 3. Brainstorm & Analyse Ideas
Bringing the team together to brainstorm and create preliminary sketches whilst ingesting all of the data that has been gathered allows us to understand how this will potentially impact the design.
Step 5. Review & Gather Feedback
Here we will present our ideas and concepts back to you. From the feedback generated we will make amendments to the concept in line with your requests.
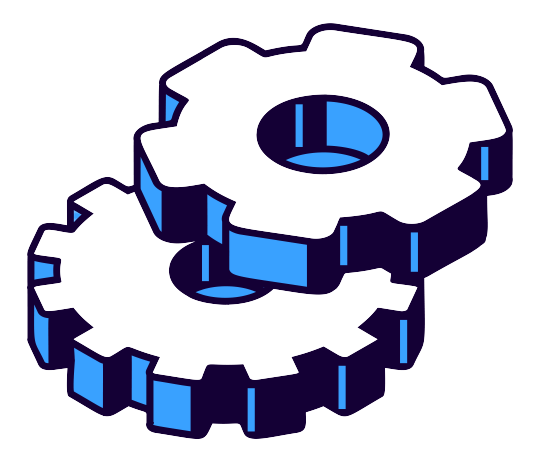
Step 2. Conduct Research And Collect Information
By researching & collecting all relevant information in form of sketches / pictures / documents, we build a solid base to work from.
Step 4. Concept Development
This is where we will create the first design solutions driven from the activity in the previous three steps. Generally offered in a CAD Solid model format.
Step 6. Completion
Final tweaks to the design are made, the completed project is handed back to the satisfied client.
We follow these 6 steps to ensure the mechanical design is optimum:
Step 1. Outline The Concept/Problem
This will enable us to have a clear idea of what the problem is before it is overcome.
Step 2. Conduct Research And Collect Information
By researching & collecting all relevant information in form of sketches / pictures / documents, we build a solid base to work from.
Step 3. Brainstorm & Analyse Ideas
Bringing the team together to brainstorm and create preliminary sketches whilst ingesting all of the data that has been gathered allows us to understand how this will potentially impact the design.
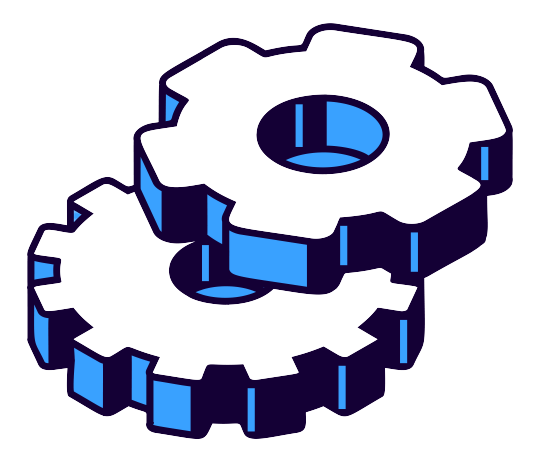
Step 4. Concept Development
This is where we will create the first design solutions driven from the activity in the previous three steps. Generally offered in a CAD Solid model format.
Step 5. Review & Gather Feedback
Here we will present our ideas and concepts back to you. From the feedback generated we will make amendments to the concept in line with your requests.
Step 6. Completion
Final tweaks to the design are made, the completed project is handed back to the satisfied client.